Polyethylen – vielseitig, effizient und nachhaltig
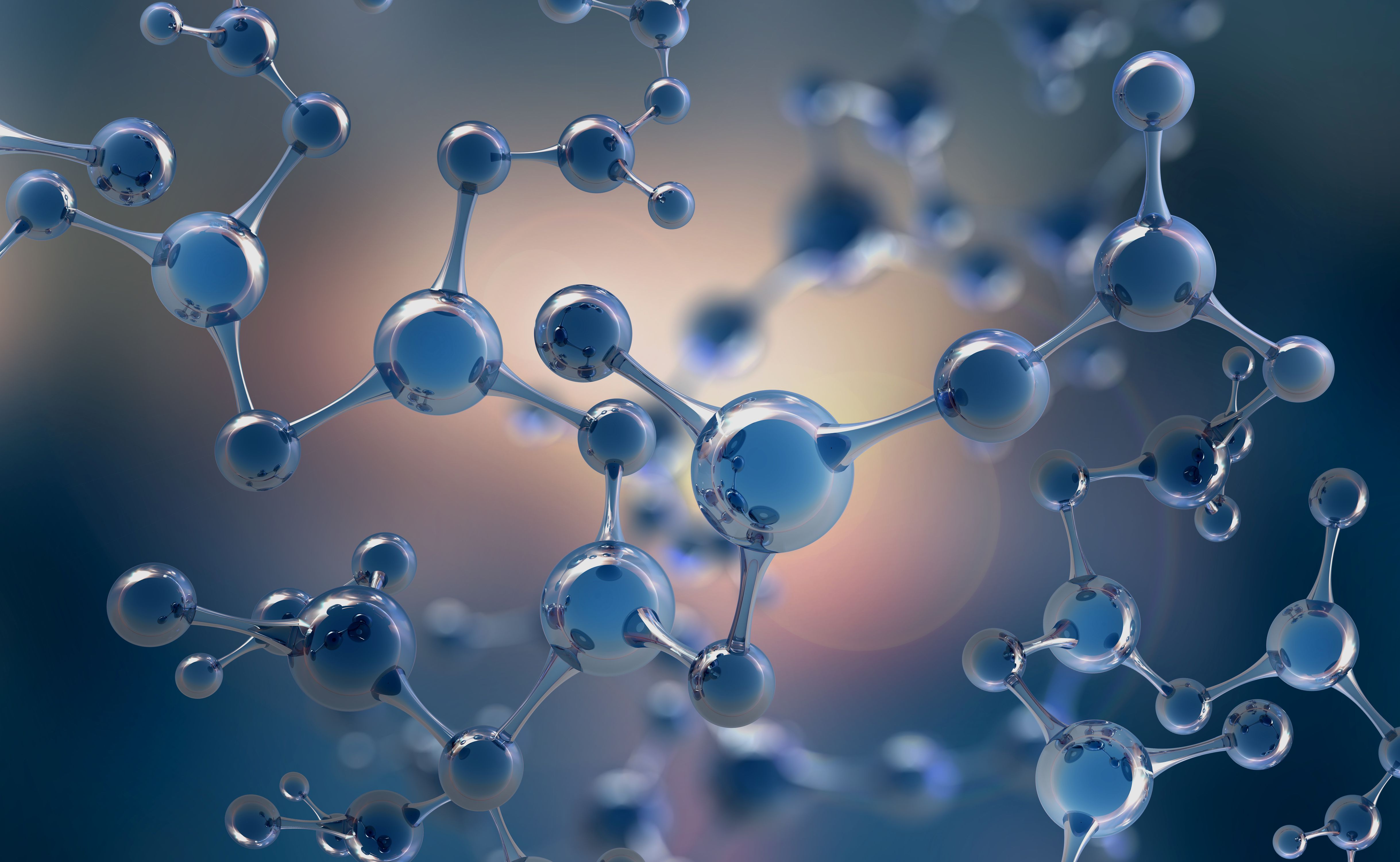
100 Jahre Makromolekulare Chemie
Erzeugt durch hoch energie-, ressourcen- und kosteneffiziente Polymerisationskatalyse aus fossilen und erneuerbaren Rohstoffen, setzt der Werkstoff Polyethylen (PE) Maßstäbe für die nachhaltige Materialentwicklung und die Kreislaufwirtschaft. Der PE-Werkstoff wird durch Innovationen in der Chemie, Katalyse, Reaktions-, Verfahrens- und Kunststofftechnik ständig neu erfunden.
Nachhaltige PE-Werkstoffe für die Kreislauf-Wirtschaft
Die Polyolefin-Werkstoffe Polyethylen (PE) und Polypropylen (PP) stehen für über die Hälfte der weltweit produzierten Kunststoffe und sind klare Spitzenreiter bei Werkstoffinnovationen, Technologietransfer, Energie-, Ressourcen-, Öko- und Kosteneffizienz. Ihre Rohstoffbasis ist flexibel und reicht von Erdöl und Gas bis hin zu Biomasse, Kohlendioxid und Polyolefinabfall. Die PE-Herstellungsverfahren durch Katalyse und Formgebung aus der Schmelze sind energiesparend und lösemittelfrei. Als hochmolekulare Kohlenwasserstoffmaterialien mit erdölähnlichem Energieinhalt können sie werkstofflich wiederverwertet oder leicht in niedermolekulare gasförmige oder flüssige Kohlenwasserstoffe zurückgespalten werden, die als Rohstoff- und Energiequelle dienen. Die Abbildung 1 zeigt den möglichen geschlossenen Kreislauf für die PE-Werkstoffe.
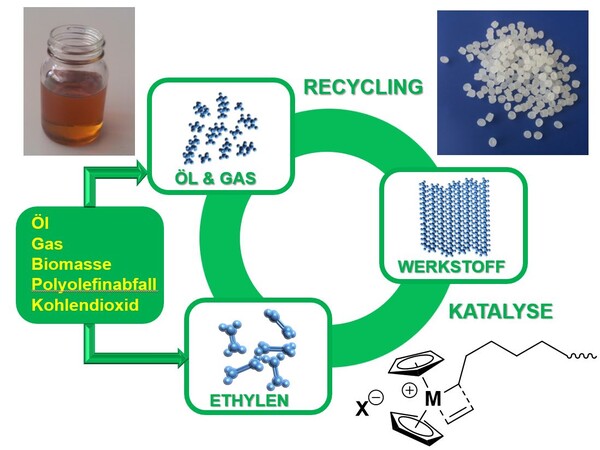
Abbildung 1: PE-Werkstoffe für die Kreislaufwirtschaft (Bildquelle: eigene Darstellung des Autors)
PE-Werkstoffe sind vielseitig
Beim hocheffizienten Verknüpfen („Polymerisation“) von Tausenden Ethylen-Molekülen entstehen lange Kohlenwasserstoffketten, deren Materialeigenschaften leicht über die Kettenlänge, Verzweigung und Nanostrukturbildung anwendungsgerecht steuerbar sind (siehe Abbildung 2). Lineares PE (HDPE für „High Density PE“) ist kristallin, schmilzt bei 135 °C und weist eine hohe Dichte (0,96 g/cm3) auf. Die PE-Ketten werden durch Verzweigung flexibel, haben geringere Kristallinität und niedrigere Dichte (LDPE für „Low Density PE“ bzw. LLDPE für „Linear Low Density PE“). Sie sind bei hoher Verzweigung sogar amorph, weich und elastisch. Aus HDPE werden ermüdungsbeständige Rohre extrudiert, während durch Blasformen von LDPE/LLDPE Folien und reißfeste Verpackungen mit geringem Gewicht entstehen. Ultrahochmolekulares PE (UHMWPE für „Ultrahigh molecular weight PE“) mit Molekulargewichten von mehreren Millionen ist für seine überragende Schlagzähigkeit und Abriebbeständigkeit bekannt, erfordert jedoch die Formgebung durch Sintern. Aus UHMWPE werden hochfeste Fasern, die Stahl übertreffen, und hoch abriebbeständige Werkstoffe für die Medizintechnik hergestellt. Hochverzweigtes PE (EPM, EPDM, TPO) ist als Gummi im Einsatz.
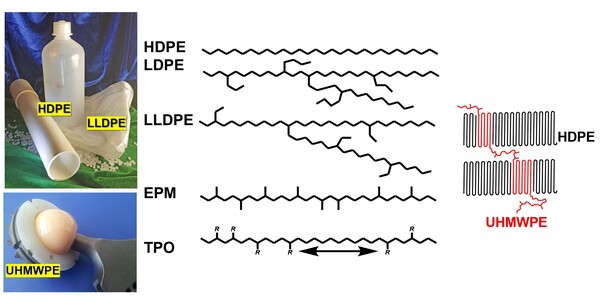
Abbildung 2: Architekturen und Anwendungen PE-Werkstoffen (Bildquelle: eigene Darstellung des Autors)
Was haben der PE-Werkstoff und Aspirin gemeinsam?
Beide wurden um 1898 entdeckt. Hier endet jedoch die Gemeinsamkeit. Damals und heute ist Aspirin identisch. Der PE-Werkstoff wird seither ständig weiterentwickelt und neu erfunden. Von Pechmann stellte 1898 erstmals PE her, doch erkannte damals niemand seine Bedeutung. Die PE-Materialien, Verfahren und Nachhaltigkeit von heute waren noch vor wenigen Jahrzenten undenkbar.
Hochdruck-LDPE
Der Firma ICI gelang im Jahr 1933 die LDPE-Herstellung durch die Ethylen-Polymerisation bei extrem hohen Drücken von über 1400 bar und hohen Temperaturen von über 150 °C. Im Zweiten Weltkrieg wurde die LDPE-Technologie geheim gehalten, da LDPE das Material der Wahl für die Kabel-Isolierungen und Abdeckungen von Radargeräten war. Durch seine Balance von Lang- und Kurzkettenverzweigungen ist LDPE attraktiv für das Blasformen von Folien und Behältern.
Niederdruck-PE durch Katalyse
In den 1950er Jahren eröffnete die Entwicklung von Katalysatoren den energiesparenden Zugang zu Niederdruck-PE (Drücke um 10 bar). Neben auf Silikagel-geträgerten Chrom- Katalysatoren („Phillips-Katalysatoren“) sind mit Aluminiumalkyl aktivierte Übergangsmetallverbindungen wie z. B. Titantetrachlorid („Ziegler-Natta-Katalysatoren“) im Einsatz. Beim Kettenwachstum („Polyinsertion“) werden Ethylen-Moleküle in die Übergangsmetall-Alkylbindung eingeschoben (siehe Abb. 2). Katalysatorinnovationen sind bis heute wichtiger Schrittmacher für die PE-Materialentwicklung.
Hohe Effizienz durch Trägerkatalysatoren
Die ersten Ziegler-Natta-Katalysatoren waren noch wenig aktiv. Korrosive und gefärbte Katalysatorrückstände sowie das wachsartige niedermolekulare PE-Nebenprodukt mussten durch Lösungsmittelextraktion abgetrennt und auf die Deponie gebracht werden. Das änderte die Entwicklung von Trägerkatalysatoren. Das Aufbringen von Ziegler-Natta-Katalysatoren auf einen Magnesiumchlorid-Träger steigerte die Katalysatoraktivität um mehrere Größenordnungen. Als Folge der hohen Aktivitäten (1000 kg PE/g Titan entspricht 1 ppm Titan im PE) kann der Katalysator im PE verbleiben. Es werden keine PE-Wachse als Nebenprodukt gebildet. Aufreinigung, Emissionen und das Deponieren von Abfällen entfallen. Heute erzeugen Trägerkatalysatoren sogar Granulat direkt im Reaktor bei der katalytischen Ethylen-Polymerisation.
Lösemittelfreie Gasphasenpolymerisation
PE der ersten Generation wurde durch Fällungs- oder Lösungspolymerisation in organischen Lösemitteln, wie z. B. Dieselfraktionen erzeugt. Mit den neuen Trägerkatalysatoren gelang in den 1970er Jahren der Durchbruch in der industriellen Gasphasenpolymerisation. Die Handhabung, das Recyclen und die Emissionen von Lösemitteln entfallen.
LLDPE und Öko-Marketing
Der industrielle Durchbruch der Polymerisationskatalyse und LLDPE-Produktion kam in den 1980er Jahren nach der Ölkrise und ist ein erster Erfolg des Öko-Marketings mit LLDPE als einer energiesparenden Alternative zum Hochdruck-LDPE. Beim LLDPE erfolgt die Verzweigung durch den Einbau von Comonomeren. LLDPE mit neuen Verzweigungsmustern ist heute mit neuen Katalysatoren direkt aus Ethylen sogar ohne Comonomerzusatz machbar. Beim „chain walking“ bleibt der katalytisch aktive Komplex nicht am Kettenende, sondern wandert entlang der Kette hin und her und erzeugt so Verzweigungen.
Ermüdungsbeständige HDPE-Rohre
Durch die Kombination von mehreren Reaktoren („Kaskaden-Reaktoren“), die Entwicklung von Reaktoren mit verschiedenen Zonen („Multizonen-Reaktoren“) und das Co-Trägern verschiedener Katalysatoren („Mehrzentren-Katalysatoren“) werden heute Molmassenverteilungen und Verzweigung unabhängig voneinander über einen weiten Bereich gesteuert. Bereits ein bis zwei Gewichtsprozente des leicht verzweigten UHMWPEs verknüpfen als molekularer „Klebstoff“ die HDPE-Kristallite (siehe Abb. 2 rechts). So steigt die Ermüdungsbeständigkeit von HDPE-Rohren um Größenordnungen. Die Haltbarkeit von HDPE-Wasserleitungen unter Druck kann deshalb heute über Jahrzehnte garantiert werden.
Einzentren-Katalyse und Eisen-Katalysatoren
In den Pioniertagen enthielten Katalysatoren verschiedenartige katalytisch aktive Übergangsmetall-Zentren mit komplexen und schwer steuerbaren Wechselwirkungen. In den 1980er Jahren hat die Entdeckung von hochaktiven Einzentren(„Single-Site“)-Katalysatoren, wie z. B. Metallocenen (siehe Abb. 1) die Katalysatorentwicklung revolutioniert. Heute sind sogar Eisenkatalysatoren für die industrielle PE-Produktion verfügbar. Über die Strukturen der Einzentren-Katalysatoren ist das molekulare Design der PE-Werkstoffe mit hoher Präzision möglich.
UHMWPE und hochfeste Fasern
UMWPE weist hohe Abriebfestigkeit und Schlagzähigkeit auf. Es ist das Material der Wahl für die Gelenkpfannen von künstlichen Hüftgelenken (siehe Abb. 2 links). Die Firma DSM entwickelte ein Gelspinn-Verfahren für die Produktion von UHMWPE-Fasern (DyneemaTM), die bezogen auf die Masse die Festigkeiten von Stahl-, Kevlar- und Kohlenstoff-Fasern weit übertreffen. Die hohe Festigkeit wird durch das perfekte Ausrichten der PE-Ketten erzielt. Das Anwendungsspektrum reicht von chirurgischen Handschuhen bis hin zu leichten schusssicheren Schutzwesten und reißfesten Seilen für Bergsteiger und Segelschiffe.
Mehrzentren-Katalyse und thermoplastische Elastomere
Copolymere von Ethylen mit Propylen oder 1-Okten sind als Elastomermaterialien bekannt und werden heute mit Einzentren-Katalysatoren weit besser als früher möglich anwendungsgerecht maßgeschneidert. Im „Chain Shuttling“-Verfahren der Firma Dow werden Polymerketten zwischen zwei katalytischen Zentren hin und her transportiert. An einem Zentrum, das kein Comonomer einbaut, werden steife HDPE-Segmente erzeugt, während am anderen Zentrum hochflexible Ethylen/1-Okten-Copolymersegmente eingefügt werden. So werden die Elastomereigenschaften eingestellt.
Grünes Polyethylen
Im Jahr 2011 begann die Firma Brazkem die Produktion von bio-basiertem PE (Green PolyethyleneTM) aus nachwachsenden Rohstoffen. Aus Zuckerrohr wird durch Fermentation Bioethanol gewonnen, das durch Wasserabspaltung Ethylen für die Polymerisationskatalyse liefert. Rohstoffe für erneuerbares PE sind heute auch durch Vergasen und Verölung von Abfällen aus Forst- und Landwirtschaft oder sogar direkt aus Kohlendioxid und Wasserstoff zugänglich.
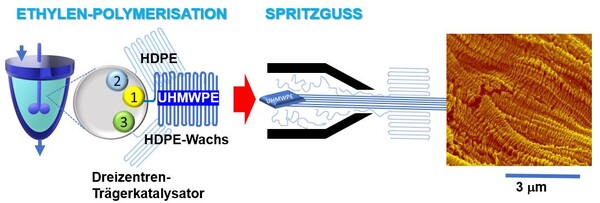
Abbildung 3: PE-Selbstverstärkung und werkstofflich recyclingfähige sortenreine PE-Verbundwerkstoffe (Bildquelle: eigene Darstellung des Autors)
Recyclingfähige sortenreine PE-Verbundwerkstoffe
Um PE zu verstärken, werden in der Regel Fremdstoffe wie Fasern und anorganische Füllstoffe zugesetzt, welche das PE-Recycling beeinträchtigen. Erst heute gelingt die Selbstverstärkung durch gerichtete Kristallisation direkt bei der Formgebung. Schlüsselkomponenten sind UHMWPE/HDPE-Reaktorblends, erzeugt mit Mehrzentren-Katalysatoren (siehe Abb. 3). Beim Spritzgießen schmilzt das nanophasenseparierte UHMWPE und bildet faserähnliche Nanostrukturen von hochorientiertem UHMWPE aus. So können Steifigkeit, Festigkeit und Schlagzähigkeit massiv gesteigert und die brachliegenden Leistungsreserven des PE-Werkstoffs mobilisiert werden, ohne die Verarbeitung zu beeinträchtigen. Erstmals ist Werkstoff-Recycling möglich, da die Nanostrukturen beim Recycling erneut ausgebildet werden.
Autor: Prof. Dr. Rolf Mülhaupt, Freiburger Materialforschungszentrum und Institut für Makromolekulare Chemie der Albert-Ludwigs-Universität Freiburg
Redaktionelle Bearbeitung: Maren Mielck, GDCh
Literatur:
T. Hees, F. Zhong, M. Stürzel, R. Mülhaupt, Macromol. Rapid Commun. 2019, 40, 1800608, “Tailoring Hydrocarbon Polymers and All‐Hydrocarbon Composites for Circular Economy”.
L.L. Böhm, Angew. Chem. 2003, 115, 5162-5183, „Die Ethylenpolymerisation mit Ziegler‐Katalysatoren 50 Jahre nach der Entdeckung“.
M. Aulbach, F. Küber, Chemie in unserer Zeit 1994,28, 197-208, „Metallocene – maßgeschneiderte Werkzeuge zur Herstellung von Polyolefinen“.
M.C. Baier, M.A. Zuideveld, S. Mecking, Angewandte Chemie 2014, 126, 9878-9902, „Post‐Metallocene in der industriellen Polyolefinproduktion“.
M. Stürzel, S. Mihan, R. Mülhaupt, Chemical Reviews, 2016, 116, 1398-1493, “From Multisite Polymerization Catalysis to Sustainable Materials and All-Polyolefin Composites”.
R. Mülhaupt, Macromol. Chem. Phys. 2013, 214, 159-174, “Green Polymers and Bio-Based Plastics: Dreams and Reality.”
Kommentare
Keine Kommentare gefunden!