Polymerdispersionen – die oft verkannten Multitalente
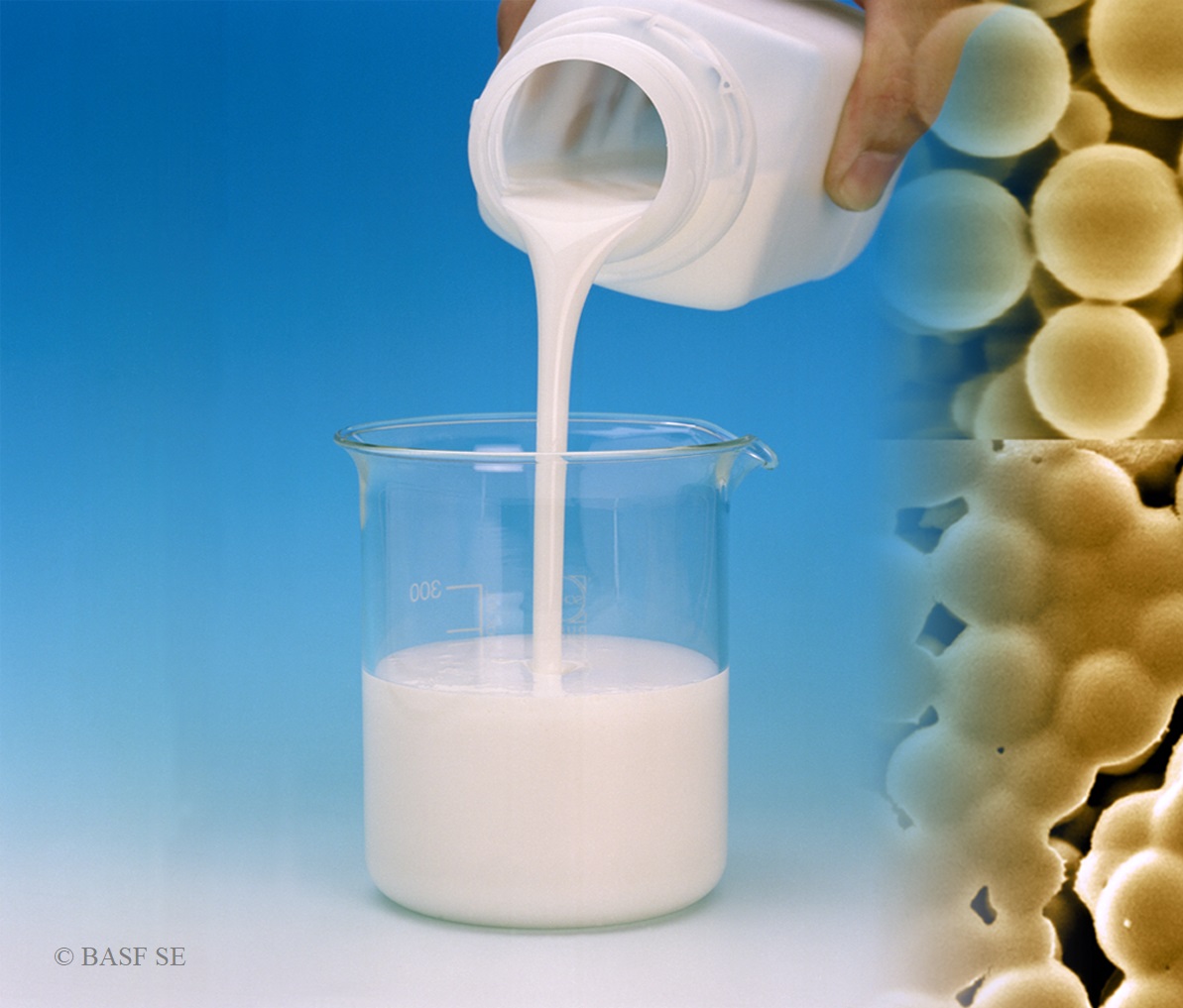
100 Jahre Makromolekulare Chemie
Wässrige Polymerdispersionen begegnen uns täglich in vielen Alltagprodukten und Gebrauchsgeständen wie Dispersionsfarben oder selbstklebenden Etiketten und sind dennoch eine recht wenig bekannte und oft verkannte Polymerklasse.
Historische Anfänge
Die ersten Versuche zu ihrer Herstellung gehen in die 1910er und 1920er Jahre zurück, also genau auf die Zeit, als Hermann Staudinger seine berühmte Arbeit über Makromoleküle ausführte. Inspiriert wurden die ersten Herstellversuche von Naturkautschuk, einer durch Proteine stabilisierten kolloidalen Emulsion von cis-1,4-Polyisopren1, mit der sich Staudinger selbst intensiv befasste2. Die Forschungs- und Entwicklungsarbeiten an Polymerdispersionen in den 1930er und 1940er Jahren konzentrierte sich in den Vereinten Staaten und in Deutschland vor allem auf die Herstellung von synthetischem Kautschuk aus Butadien und Styrol (GR-S Rubber, Buna-S) sowie aus Butadien und Acrylnitril (Buna-N)1.
Eines der frühen BASF-Patente zur Polymerisation von mit Seifen emulgierten Acrylatmonomeren aus dem Jahr 1930 geht auf Hans Fikentscher zurück3. 1931 wurde die erste Acrylatdispersion für die Lederzubereitung vermarktet. Acronal® 500D, eine Butylacrylat-Vinylacetat-Copolymerdispersion für die Papierveredelung, stammt aus dem Jahr 1941 und wird noch heute produziert. Aus diesen Anfängen entwickelten sich im Lauf der Jahrzehnte ganze Produktfamilien mit sehr spezifischen Eigenschaftsprofilen, die auf die verschiedenen Anwendungen und Verarbeitungsprozesse zugeschnittenen sind.
Herstellung von Polymerdispersionen
Die Herstellung von Polymerdispersionen, die im englischen Sprachgebrauch meist als „Polymer Latexes“ bezeichnet werden, erfolgt nach dem Verfahren der Emulsions-polymerisation. Dabei wird eine mit Tensiden oder polymeren Schutzkolloiden stabilisierte wässrige Emulsion von Monomeren mit einem wasserlöslichen Radikalstarter wie beispielsweise Ammoniumperoxodisulfat polymerisiert. Neben hydrophoben Monomeren wie etwa MMA, Styrol oder n-Butylacrylat werden oft auch geringe Mengen hydrophiler Monomere wie z.B. Acrylsäure oder Acrylamid eingesetzt. Letztere tragen neben den eingesetzten anionischen und nichtionischen Tensiden zu einer zusätzlichen elektrosterischen Stabilisierung der entstehenden Polymerdispersionsteilchen bei.
Mechanistisch startet die Polymerisation mit dem thermischen Zerfall des Radikalstarters in der Wasserphase. Dort werden auch die ersten Monomere an das Initiatorradikal addiert bis das wachsende Oligomerradikal eine kritische Kettenlänge als auch Hydrophobie erreicht und in eine der Tensidmizellen diffundiert. In dem hydrophoben Inneren der Mizelle addiert das Polymer weiteres Monomer, das durch Diffusion aus den Monomertröpfchen durch die Wasserphase nachgeliefert wird. So entstehen und wachsen die Polymerketten zu Dispersionsteilchen, die am Ende der Polymerisation je nach Rezeptur einen Durchmesser im Bereich von ca. 100 und 1.000 nm haben. Übliche Polymergehalte liegen zwischen 40 und 65 Gewichtsprozent.
Im großtechnischen Maßstab wird die Emulsionspolymerisation meist im sogenannten „Semi-Batch“-Verfahren durchgeführt. Hierbei wird die Emulsion der Monomere über einen Zeitraum von wenigen Stunden in einen gerührten Polymerisationsreaktor eingebracht.
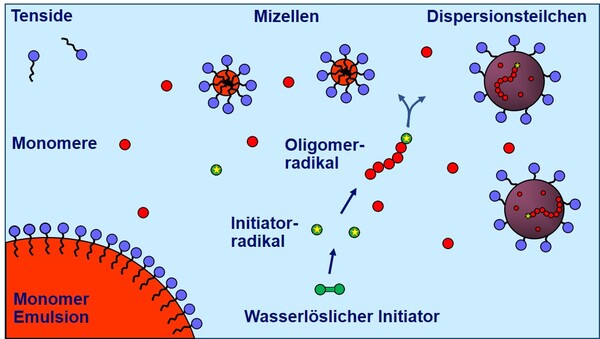
Abb. 1: Mechanismus der Emulsionspolymerisation, © BASF SE
Durch die Polymerisation in den mikroskopisch kleinen Polymertröpfchen lassen sich sehr hohe Molekulargewichte und Polymergehalte bei vergleichsweise niedriger Produktviskosität herstellen. Dies ermöglicht die sichere Abführung der Reaktionswärme aus der stark exothermen radikalischen Polymerisation über den Kühlmantel des Reaktors. In ein und derselben Anlage lassen sich durch Variation der eingesetzten Monomere, der Zusammensetzung und der Prozessbedingungen sehr viele verschiedene Copolymere für unterschiedlichste Anwendungen herstellen. In diesem Punkt ist die Emulsionspolymerisation zweifelsohne eines der flexibelsten technischen Herstellverfahren für Polymere.
Struktur-Eigenschaftsbeziehungen und Anwendungen
Nach den verwendeten Hauptmonomeren unterscheidet man drei Haupttypen von Polymerdispersionen: Acrylat-Dispersionen, Vinylacetat-Dispersionen und Styrol-Butadien-Dispersionen.
Mit den technisch verfügbaren Monomeren lässt sich über entsprechende Copolymere ein sehr breiter Bereich der Glasübergangstemperatur (Tg) von etwa -50 °C bis +100 °C abdecken, so dass vielfältige Anwendungsbereiche zugänglich sind4. Pro Jahr werden weltweit etwa 25 Millionen Tonnen Polymerdispersionen produziert, wovon knapp die Hälfte auf Acrylat-Dispersionen entfällt. Vinylacetat- und Styrol-Butadien-Dispersionen stehen jeweils für etwa 25 % dieser Menge.
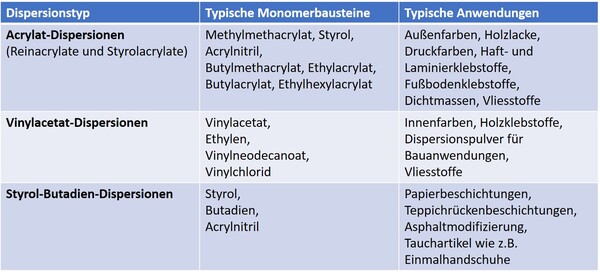
Abb. 2: Monomerbausteine und Anwendungen von Polymerdispersionen, © BASF SE
Neben den genannten Hauptmonomeren spielen für die Einstellung der gewünschten Verarbeitungs- und Anwendungseigenschaften auch noch die in kleinen Anteilen eingebauten funktionalen Monomeren eine sehr wichtige Rolle. Das sind zum einen die Säuregruppen enthaltenden Monomere wie etwa Acrylsäure, Methacrylsäure und Itaconsäure, welche für die kolloidale Stabilität der Dispersionen, aber auch für die Wechselwirkung mit Pigmenten und Füllstoffen in Farben wichtig sind. Zum anderen sind das reaktive Monomere wie beispielsweise Glycidylmethacrylat, Acetoacetoxyethylmethacrylat, 3-(Trimethoxysilyl)-propylmethacrylat oder Diacetonacrylamid, die über eine chemische Nachvernetzung nach der Filmbildung die mechanischen Eigenschaften und Beständigkeit der Dispersionsbeschichtungen verbessern.
In praktisch allen Anwendungen werden die Polymerdispersionen flüssig appliziert und durchlaufen dann beim Trocknen den Prozess der Filmbildung, bei dem die individuellen Dispersionspartikel zu einem homogenen Film verschmelzen5:
Neben der Eigenschaftssteuerung über die chemische Zusammensetzung der Polymerdispersion bietet das Verfahren der Emulsionspolymerisation noch eine Vielzahl von Möglichkeiten der Eigenschaftssteuerung über Prozessparameter. Zum Beispiel können verschiedene Morphologien der Dispersionsteilchen durch eine Stufen- oder Gradientenfahrweise eingestellt werden. Dabei wird die Zusammensetzung der zugefahrenen Monomeremulsion in Stufen oder in einem Gradienten verändert. So entstehen unterschiedliche, nicht verträgliche Copolymere, die sich während der Polymerisation z.B. zu Kern-Schale-Partikeln mit harter Schale (hohe Tg) und weichem, flexiblem Kern (niedrige Tg) entmischen. Auf diesem Weg lassen sich Bindemittel für hochflexible und dennoch blockfeste Holzbeschichtungen herstellen.
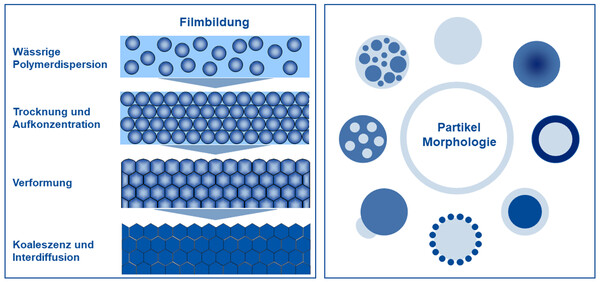
Abb. 3: Verschiedene Partikel Morphologien und Mechanismus der Filmbildung von Polymerdispersionen, © BASF SE
Auch einhundert Jahre nach ihren allerersten Anfängen erweisen sich die umweltschonenden wässrigen Polymerdispersionen immer wieder als wahre Multitalente, mit denen sich neue und unerwartete Eigenschaften erzielen lassen; beispielsweise um lösungsmittelhaltige Bindemittel und Klebstoffe aus ihren angestammten Anwendungen zu verdrängen. Auf diese Weise tragen wässrige Polymerdispersionen wesentlich dazu bei, nachhaltigere Lösungen für viele Anwendungen zu finden und Emissionen zu verringern. Moderne Charakterisierungs- und Modellierungsmethoden sind dabei heutzutage zu unverzichtbaren Hilfsmitteln geworden.
Autor: Dr. Bernd Reck,
BASF SE, Ludwigshafen
Redaktionelle Bearbeitung: Maren Mielck, GDCh
Literatur:
A.M. van Herk (editor), Chemistry and Technology of Emulsion Polymerization, 2nd Edition, Wiley (2013)
H. Staudinger, J. Fritschi, Über Isopren und Kautschuk. 5. Mitteilung. Über die Hydrierung des Kautschuks und über seine Konstitution, Helvetica Chimica Acta, 5, 785–806 (1922)
Hans Fikentscher, Claus Heuck, US 2.123.399 (1930) für IG Farbenindustrie AG, Ludwigshafen
D. Urban, K. Takamura (editors), Polymer Dispersions and Their Industrial Applications, Wiley-VCH (2002)
J.L. Keddie, A.F. Routh, Latex Film Formation, Springer (2010)
Kommentare
Keine Kommentare gefunden!